Over the last 12 months, Nippon Gas Company (NICIGAS) has been upgrading its existing meters across Japan by attaching an IoT-based reader called Space Hotaru that would allow remote collection and transmission gas consumption data – in one of the largest smart utilities deployment to date.
In an exclusive interview, FutureIoT spoke with Philippe Chiu, co-founder and chief technology officer of UnaBiz, about the smart meter project in an in-depth interview that covers the impact of COVID-19, the importance of supply chain, challenges around customisation and integration and more.
Singapore-based UnaBiz is the product design and hardware device manufacturer, who together with SORACOM, developed the Space Hotaru from NICIGAS’ original concept.
(First of three parts)
UnaBiz aims to complete the installation of the first batch of 850,000 units of NICIGAS’ Space Hotaru by March this year.
Checking the real-time dashboard that tracks the deployment process in late January, Philippe Chiu, company co-founder and CTO, said approximately 720,00 units have been connected and even now are already transmitting data back to NICIGAS.
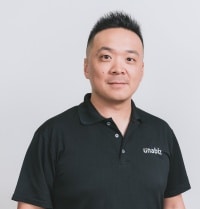
“The actual figure is just a figure, but what matters in the end is that it's progressing as planned, which is by itself an achievement. We’re only a hundred thousand units away from our first milestone,” Chiu said.
The NICIGAS project was spurred by the Japanese government’s push for the standardisation and “smartification” of gas meters across the island nation. In fact, gas meters in the country are designed to automatically switch off when triggered by external events such as earthquakes.
“The issue is that these smart features are in tech, we say local, which means that there is no remote or wireless activation or deactivation of those meters. Thus, you could have meters that have been switched off and without NICIGAS knowing about it,” Chiu said.
In the past, the utility company would heavily rely on manpower to check deactivated meters; and delays would be inevitable as company staff had to physically go onsite to thoroughly inspect each unit. However, this typical task could be optimised and enhanced using remote access that Space Hotaru seeks to deliver.
A year of development
It took UnaBiz a full 12 months to finetune the Space Hotaru and get it ready for deployment. According to Chiu, to getting the shape of the device right is only part of the process.
“Just having a device that shape doesn't take a year, but it's all the different phases of testing, validation, reliability testing. The full development started Q1 2019, and production line was ready on Jan 2020,” Chiu said.
He recalled: “Our prototype was out after two months, from nothing to a lot of ideation and how it would look like etc. The whole project had at least ten different types of shapes and you have 10 different proposals justifying each design. We compress that time and made a decision in just a little over two months.”
After the design of the device was approved, the team proceeded in the next eight to 10 months to conduct testings, reliability certifications that includes the factory set up, all the different quality checks involving different aspects of the device.
Grappling supply chain challenge caused by COVID 19
UnaBiz started production of the Space Hotaru in early 2020 with the first trial run conducted before Chinese New Year. Everything was running smoothly with the rate of production and shipping was planned for the rest of 2020.
In early February, the initial impact of the COVID-19 hit on the global scales. Factories closed as governments imposed citywide lockdowns.
“Everything planned perfectly became a huge question mark. It is uncertain when everything is going to resume, everything is under lockdown and we're not pushing because it's a health and safety issue. It's dangerous, we're talking about people's lives and that was a huge question mark, which created quite some delay and uncertainty. We have been spending a whole year on R&D, and finally seeing it happening and then you take one of the largest crises worldwide,” Chiu said.
Like most technology companies, UnaBiz has multinational operations that require a highly synchronised supply chain.
While the company is headquartered in Singapore, its R&D and manufacturing partners are located in Taiwan, the port is in Hong Kong, the manufacturing is being done in China and the customer is based in Japan.
“Never underestimate the deployment. Having such volume in tens of thousands at international level, you realise very realistically and concretely the importance of physical logistics and supply chain.
“IoT is really much more than just a bunch of youngsters having great ideas and saying, I'm going to do a lot of things with your data. The fact is so many things can go wrong, with that international way of doing things. You could just ask DHL to do that, but it would be way too expensive for you to manage. The customer won’t pay, so there's no deal. The rollout plan and the supply chain is key in such projects, without that no project for everyone,” Chiu said.
UnaBiz has a fully dedicated supply chain team of roughly 15 people – comprising one quarter of the company headcount – doing the supply chain, buying components and making sure they reach the right points at the right time to avoid delays.
"We do have a second and third layer of factories, some being not in China. Post-COVID and given that we have much more to produce, we definitely need to have alternative locations. I cannot explicitly mention where it is, but it is still in Asia, and it's definitely not in the same country as the main factory, where we did the first batch. It's a very common practice in the industry, which is called multi-sourcing. So, that is in place even for factory," Chiu said.
Getting deployment back on track
The lockdowns of COVID-19 was a huge setback for the deployment schedule, but Unabiz learned how to roll with the punches.
“We gained a lot of maturity from that managing the chaos. We had to know how to deal with that new situation of uncertainty, which is much more complex than Amazon or Lazada, where you click order and you have it the next day,” Chiu said.
UnaBiz experienced a few weeks of delays and it had to recover this lost time to keep deployment on schedule.
“The challenge happened on the production side of things. This is where we are kind of proud of having put the right resources on the right places years ago to have that know-how. This is where the team was challenged. Years ago, people were asking us why we put so much efforts on supply chain, you just call a factory, tell them to manufacture the thing. It can work on other years, but last year was a no go. And this is where we were really happy, as it confirmed the right investment of having that very experienced and agile supply chain team,” Chiu said.
He added: “Obviously, we had some hit and miss and convicted almost two months delay in the whole schedule, which is not so bad given now that we know it was a crazy situation. But in the industry, two months delay is huge.”
UnaBiz credits its strong relationship with NICIGAS for being able to weather this supply chain storm.
“This is why we are not calling NICIGAS a customer, but rather a partner as we're in this together. The challenge was strong, but thankfully our partnership or internal structure was strong enough to recover from that. It took us eight months to catch up on these two missing months. It was definitely not easily, and frankly, if you ask me would we expected to have so much strain on the supply chain, it is clearly no. However, it was a good test. UnaBiz tends to specialise on massive, high volume of connected products, which is why we are facing such kind of issues. A low volume is still fine, but when you order tens or hundreds of thousands, then it's a completely different ballgame,” Chiu said.
To be continued: Value of customisation and integration in massive IoT projects