Two of Hong Kong’s well-established food manufacturers, Lee Kum Kee (Hong Kong) Foods Limited and Leun Tai Hong Kong Fresh Liquid Eggs Limited, will set up a new smart production line as part of their industry 4.0 transformation – in projects partially financed by the city’s Re-industrialisation Funding Scheme (RFS).
Lee Kum Kee (Hong Kong) Foods Limited has earmarked HK$46 million to build its new oyster sauce smart production line, which is scheduled to start operation in the first quarter of 2024.
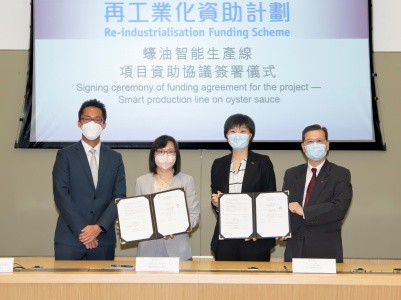
The new fully automated production line will produce 20,000 bottles of oyster sauce per hour, doubling the production capacity of the company's oyster sauce manufacturing plant at Tai Po InnoPark. Artificial intelligence (AI) will be deployed in the new line to monitor the production process and to gather real-time data to enhance product traceability and overall operational efficiency.
The company last week received HK$15 million under the RFS to partially fund the project.
“We are glad to receive funding support for our new Oyster Sauce Smart Production Line project under the RFS. We are committed to implementing digital upgrade and smart factory transformation, in order to enhance our production efficiency and satisfy consumer needs,” said Kathy Lam, CEO, Lee Kum Kee International Holdings.
Launched in July 2020 under the auspices of the city’s Innovation and Technology Commission (ITC), the RFS provides subsidy to manufacturers in Hong Kong who are upgrading their factories into smart production lines. The scheme offers a matching financial support amounting to one-third of the approved project cost, capped at a maximum ceiling of HK$15 million per project. Projects under the scheme are expected to be completed within 24 months.
Upgrading production processes
Lee Kum Kee (Hong Kong) Foods is the latest local food manufacturer to avail of the RFS initiative.
In January of this year, the ITC approved a HK$14.9 million RFS project to help Leun Tai Hong Kong Fresh Liquid Eggs Limited to establish its smart production line for its fresh liquid egg products. The new smart facility will be similarly located at the Tai Po InnoPark.
The smart production line project is expected to increase the daily production of fresh liquid eggs by two to three times, while lowering the production cost by 20% to 30%.
Established in 1957, Luen Tai Hong is a key local supplier of fresh liquid eggs (with a market share of nearly 30%) for many restaurants and food manufacturers in Hong Kong. It established the first pasteurised liquid eggs factory in the city in 2013.
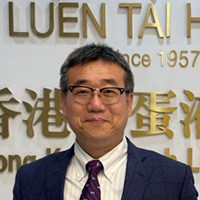
Leun Tai Hong last month has enlisted the help of the Hong Kong Productivity Council (HKPC) to customise the design of its new smart production line.
“At present, 30 tons of fresh egg liquid are produced every day, mainly relying on manual supervision and productivity is limited. With intelligent production, the production capacity can increase by 2 to 3 times, with 60 to 70 tons of fresh egg liquid to be produced per day,” said Young Kam-yim, managing director of Luen Tai Hong.
He added: “At the same time, manpower, production time and human error will be reduced, achieving overall cost saving of up to 30%. Staff can also be deployed to handle high-tech work, reducing costs and raising efficiency. Intelligent production will also diversify our business. In addition to expanding from B2B to B2C retail business, high production capacity will also help the brand enter the huge and potential Greater Bay Area (GBA) market with a population of more than 86 million, making Hong Kong’s food manufacturing industry shine on the global stage.”
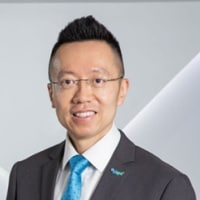
By applying HKPCs one-stop integrated technical support, Leun Tai Hong will be able to optimise its production process through the adoption of sensors, Internet of Things and machine vision. Furthermore, the production process will be monitored with real-time data to ensure product safety and traceability, while increasing productivity and stability.
“The food industry is one of the top four sectors boosting the largest value growth among local manufacturing. We determined to lead the food industry gradually move towards advanced manufacturing so as to strengthen the ‘Made in Hong Kong’ brand and let it shine in the international market,” said Edmond Lai, chief digital officer, HKPC.
He added: “With the advanced manufacturing technologies of i4.0, HKPC helps the manufacturing industry to streamline the traditional production process. Through data-based real-time monitoring of product quality, operators can also flexibly deploy according to the data of each position, and establish predictive maintenance to avoid losses incurred by unexpected downtime, making enterprise management more handy.”