I was reading one of Gartner’s surveys on supply chain transformations and found that 44% of them achieve half, or fewer, of the initiative’s targeted benefits.
That’s a big number!
It’s especially large when you consider that most organizations are trying to stabilize, pilot or get approval to change their planning tools.
Proportion of Supply Chain Transformation Benefits Achieved
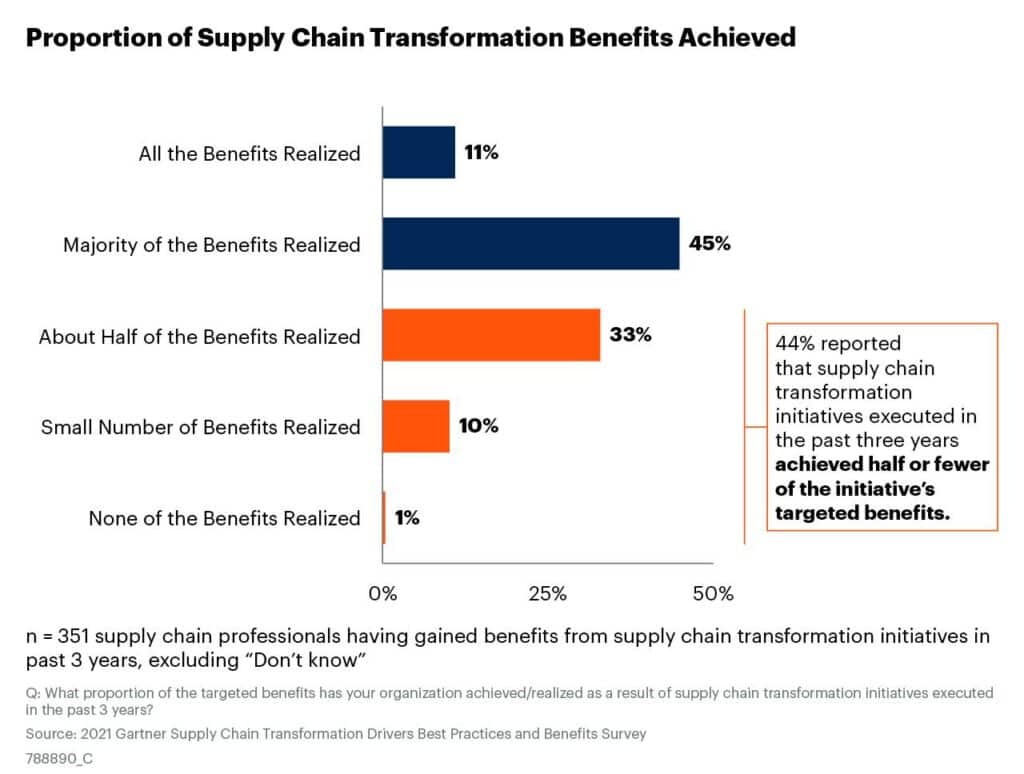
When trying to think about what is missing, or why so many are failing to adopt new technology, the main theme that comes up is that most organizations are trying to implement a solution based on current processes and ways of working. Technology enables a transformation of your operating model that includes processes and organization. But shouldn’t your mindset evolve as well?
When I started working in planning, the first thing I learned was that if our company’s plans were precise everything would work out. I just needed the magic number that would make everything flow.
If only life would be so easy.
The reality is that even when you set a magic number, plans always deviate. Things are dynamic. You most likely don`t have exact plans in other areas of life. Then why do you keep focusing on a single number that will make — or, more likely, break — your supply chain plans?
As companies invest in technology, they should invest in changing the mindsets within their organizations from the obsession with a single forecast to using a range of possibilities.
Range of Possibilities
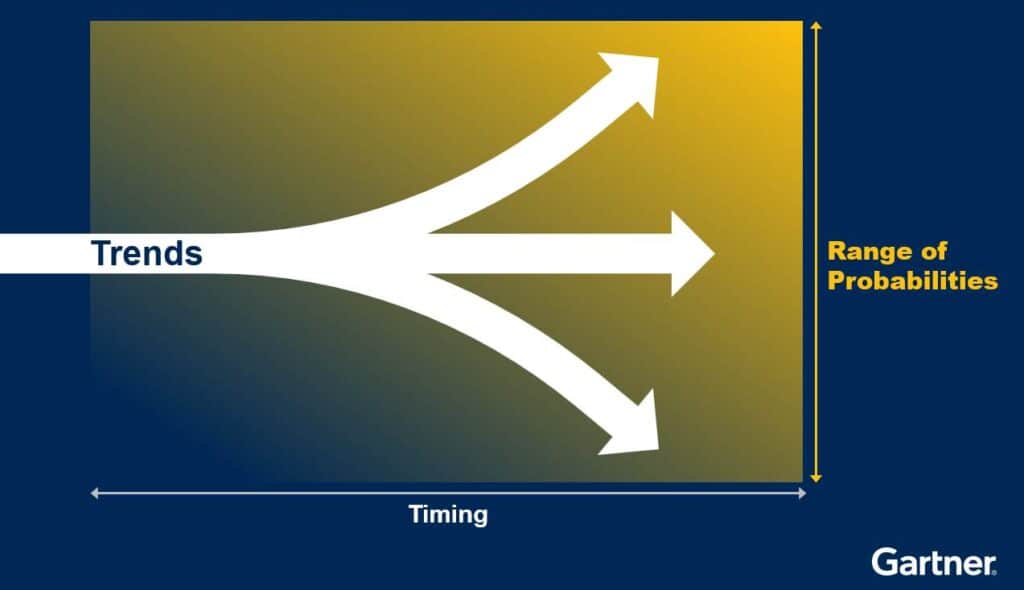
Assuming that all you need is a single plan that will make everything work is like assuming that the exact optimal circumstances will always occur. But that’s not true. The exact internal and external dynamics will rarely come together in the exact right way. By assuming all you need is a single plan, a single number, organizations make their supply chains fragile. Anything that goes above or below that number will register as a surprise.
And from that point, you know the story. … You rush in with emergency teams, firefighting these new situations as they impact your business results. Let’s face it, anytime you expedite deliveries or steer inventory due to the plan going awry it will impact your cost to serve. In fact, organizations report that they suffer a 4% increase in the cost to serve for every disruption. And they have at least five disruptions per year. So, at minimum, you’re talking about a 20% hit to the P&L.
By changing your mindset to plan for a range of possibilities and probabilities you’ll be better prepared for what will most likely occur. You can’t rely on being precise. There is a range of options from variability of lead time to variability of product mix to variability in order placement. In fact, by abandoning the idea that you must be precise, you can plan for most of the possible options you might face.
Even if you do plan for a range of possibilities, will all of them be right? Of course not. Only one option will be correct. The rest of them will be wrong. Embrace the idea that you will be wrong most of the time. Think of it this way: you have to be wrong to be right.
Now, I know that nobody likes being wrong. Because everybody wants to avoid errors, they avoid taking risks. But if you avoid risk, then how are you going to win? From Gartner’s most recent survey of supply chain technology user wants and needs, we found that 38% of those surveyed are not encouraged to take risks. Within that group, 12% are actively discouraged from taking risks.
As supply chain planning leaders, you must actively work with your teams to change this point of view.
Just like you’re investing in processes and technology, you need to make an investment in change management — you must embrace a new mindset. You can’t adopt a different operating model and new tools but continue to be stuck in your old way of thinking. If you are planning to transform your supply chain — or even if you’re in the middle of such a transformation — change your planning approach and you will be more than halfway there.
First published on Gartner Supply Chain Insights