China-based Shenyang Aluminium & Magnesium Engineering & Research Institute Co. (SAMI), a digital technology solutions provider, made waves for its first plantwide and full-stage application of digital twin technology on an aluminium plant.
Through collaborating with infrastructure engineering software company, Bentley, SAMI created a complete digital model for a RMB 3.9-billion, 750 000 square meters aluminium factory of Shanxi Chinalco China Resources Co., Ltd.
Digital Twins technology, according to an article by AL Circle “creates a virtual replica of physical equipment, processes, or systems… such as smelting furnaces, conveyor systems, and other machinery in the aluminium industry.”
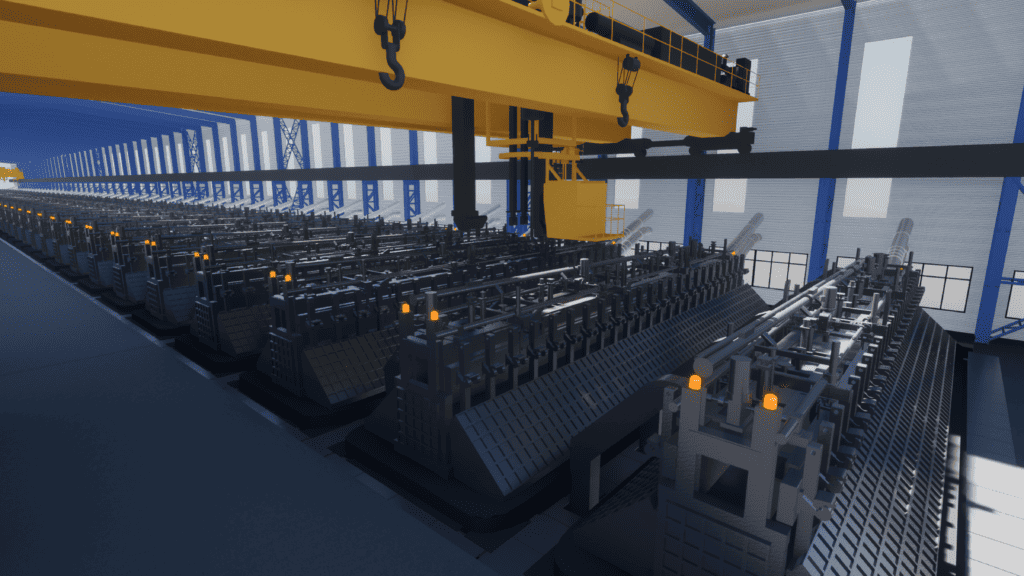
Sensors and physical records of design specifications are paired with the digital twin for the collection of real-time data from the actual equipment.
Digital twins can generate real-time insights and recommendations that can improve data interaction, access to information, decision-making, operational efficiency, and equipment monitoring.
It can also aid in resolution planning, workflow management, visualisation, simulation, projecting future changes, and cost-efficiency.
Resolving challenges
Before venturing into a digital twin application project of electrolytic aluminium engineering, SAMI encountered challenges in their workflows.
Fangbo Liu, the Project Operation director of the Digital Engineering BIM Centre of Sami, says one of their biggest challenges is learning to make use of 3D software in a short period.
“How can we quickly establish a huge plant and a big factory? How do we get this data during the modelling stage? How do we put these into the model?”
He explains that the construction phase in China is usually very short; they knew they needed to use digital technology to improve their efficiency and quality.
Liu also recalls being challenged with improving their Operations and Maintenance (O&M) and efficiency. He says they needed “to reduce cost, reduce the burden onto the environment, and reduce energy consumption” pushing them to explore new technologies.
Practical benefits
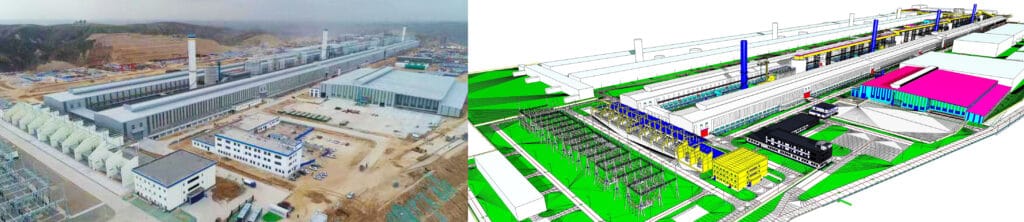
Liu recalls resolving design and quality issues SAMI encountered through the digital twin method. He says the technology ensured accuracy, especially when some of their devices had collision problems with factory devices.
“With this digital twin technology, our engineering output can precisely know how much materials we need, how much reinforcement, how much steel, how much pipes, etc. It is very precise. This is a great benefit for the construction of a factory.”
He adds that the technology enables them to monitor their construction progress.
“For construction, I will work on the model and simulate it. It makes my construction more efficient and effective.”
Through Bentley Open Applications, SAMI developed a virtual reality (VR)-based simulation and training system. Liu says it helps them integrate VR technology in training their employees to enhance onsite and inspection safety.
Liu says the technology also allowed them to build a digital management system.
“I can select a device or facility and know who produced that facility, who installed it, the problems during installation, the current status, and the relevant related materials needed.”
Reaping the rewards
Reports show that Shanxi saved six million yuan, or a reduction of 10% in its management costs through digital twin tech. A 40% reduction in the company’s non-predictive equipment failures and more than 15% improvement in efficiency saving 200 working days, compared with the traditional three-dimensional plant design, were also logged.
Further, the project led to a decrease in fluoride emissions by 5% and, headcount reduced by 10%, saving RMB 1 million in annual labour costs.
Since starting the project’s 3D design in 2017, it took 5 years for it to reach the final implementation of the digital twin plant operation and maintenance application in 2022. Half a decade of efforts won SAMI an award in the Bentley Systems 2023 Going Digital Awards in the Process and Power Generation category for its outstanding contributions to infrastructure design, construction, and operations.
Next steps
In line with China's recent promotion of the digitalisation of factories, Liu says it is a ripe time to explore digital technologies to enhance management efficiency. He looks forward to a future where SAMI will not only be known for deploying technology in design and construction but also expand in the field of O&M.
“In the past, we were never involved in O&M. Now that we have this technology, we can provide digitised O&M services to our customers,” he says. Liu says in the future, SAMI desires to continue to advocate for digitised deliverables, strengthen its technology deployment, and expand its market overseas.