In recent years, labour shortages due to the aging of skilled workers and a decline in the number of younger workers have become urgent issues for the construction industry in Japan.
As a result, labour-saving measures to enhance productivity have become a pressing issue. As such, many have called for the automation of the industry – especially for the development of technology to automate heavy machinery that is currently operated by technically skilled workers.
This vision has become one step closer to reality.
Last week, Obayashi Corporation, NEC Corporation and Taiyu Co. have announced that they jointly developed an autonomous backhoe operation system that automates sediment loading as an important step in the autonomy of construction machinery.
The three companies have capitalized on their collective experience and technological know-how. As an important first step, the companies have developed an autonomous operation system for backhoes.
The system is scheduled to be applied at a civil engineering site managed by OBAYASHI in December this year.
Pilot test
The autonomous backhoe operation system automatically carries out sediment loading, which represents a large amount of work for civil engineering projects, such as tunneling, underground excavation for large-scale buildings, and other purposes. Sediment loading requires a high degree of skill in order to effectively control backhoes' arms, booms, and buckets, making it difficult to achieve autonomy.
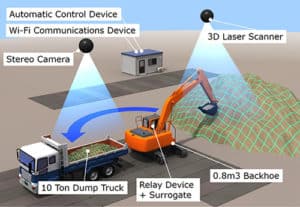
NEC applied its Adaptive Predictive Control Technologies to a general-purpose remote-control device, the surrogate, which was jointly developed by OBAYASHI and TAIYU, for installation on backhoes.
This system combines OBAYASHI's know-how of sediment conditions and dump trucks in order to perform controls that consider backhoe dynamics and constantly changing conditions. In addition, the use of know-how of technically skilled workers and AI technology has enabled the highly accurate remote control of actions conventionally carried out by technically skilled workers, such as excavation and loading.
Some key features of the autonomous backhoe operation system include the following:
1) Accuracy, safety and high productivity
The autonomous backhoe operation system uses 3D scanners to check the status of embankments in an excavation area. The system determines the points at which the amount of sediment loaded per excavation is maximized, excavates the sediment, swivels to a dump truck standing by, and repeatedly loads the dump truck while monitoring progress by camera.
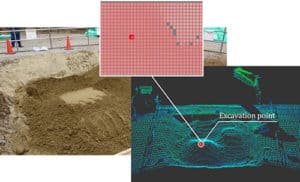
In order to improve the accuracy of operations, the system produces a series of optimal operation plans and utilizes NEC's Adaptive Predictive Control techniques to understand the dynamic characteristics of the backhoe. In addition, the system analyses the work data of a large number of skilled technicians to quantify the efficiency of their operations, in addition to analysing sediment conditions, correct it according to the position of the dump trucks or backhoes, and other conditions in order to realize higher productivity.
When the sediment loaded into a dump truck reaches a specified weight, work stops automatically until another dump truck arrives. Therefore, it is not necessary for personnel to enter a worksite, which helps to ensure safety as well as productivity. In the unlikely event of a worker's entry, Obayashi has installed the "QuattroEyes" system, which was developed by Obayashi, to ensure safety by preventing contact through fail-safe measures.
2) Easy autonomy compatibility
This system enables backhoes to be operated through a general-purpose remote control, the surrogate, developed jointly by Obayashi and Taiyu. The surrogate is attached to the control levers of a backhoe and is compatible with any manufacturer or model. Therefore, the autonomous backhoe operation system can be mounted on any commercially available backhoe, regardless of the type of the system. Since automatic operation and remote control can be easily implemented or removed, it is possible to quickly and flexibly respond to sudden events or complicated operations that require manual control as well.
3) Integrated control system that saves labour resources
The autonomous backhoe operation system is managed by a networked control system that integrates and controls a large number of sensors for recognising the conditions of work areas and construction machinery. Therefore, it is possible for the administrator to remotely check and manage large amounts of information from multiple viewpoints.
In the future, 5G – the next-generation communications, will enable faster, larger-capacity, and lower-delay communication, allowing multiple types of construction machinery to operate autonomously at the same time, helping to further improve productivity and labour savings.
What lies ahead
Going forward, Obayashi will promote the development of next-generation construction production systems capable of realizing high-productivity and high-safety even with few technicians. In the future, the company aims to contribute to solving the shortage of technically skilled workers problem in the construction industry through sales of these systems.
NEC will leverage the results of this collaboration to develop solutions that can be used to improve the efficiency and safety of construction work. Moreover, NEC will utilize network flexibly to accelerate the provision of "NEC Smart Connectivity," which dynamically links data to people and goods as it creates new social value.
And Taiyu aims to promote the expansion of remote and autonomous operations for a wide range of construction equipment through the training of skilled operators, development of surrogates and other innovative new technologies.