Mitsubishi Electric and the National Institute of Advanced Industrial Science and Technology (AIST) have developed an AI technology that predicts changes during automated manufacturing processes and then makes real-time adjustments in the factory-automation (FA) equipment, such as motion speeds among others during operation.
In addition to eliminating the need for time-consuming manual adjustments, the AI estimates the confidence level of inferences regarding factors such as machining error and then controls the FA equipment based on suitable levels of confidence. The technology is expected to lead to more stable, reliable and productive operations, particularly in agile manufacturing.
“Operating needs change frequently in agile production, so optimum conditions, such as FA equipment motion speeds, revolutions, etc., must be adjusted individually for each type of product,” Mitsubishi Electric in a statement. “Performing such adjustments manually, however, requires labour and time, resulting in decreased productivity. Moreover, declining birth rates and aging populations in many developed countries are resulting in a shortage of skilled workers capable of adjusting FA equipment.”
This is the latest deployment of an AIST AI technology in Mitsubishi Electric’s FA equipment since the two companies began collaborating on AI development in fiscal 2017.
Moving forward, Mitsubishi Electric expects to increasingly incorporate various forms of its Maisart AI technology in FA equipment and systems to significantly improve manufacturing productivity.
Key features
- Fast: AI achieves high-speed inferences for dynamic control of FA equipment control
In factories that use FA equipment for agile manufacturing, such as computerized numerical controller (CNC) cutting machines and industrial robots, the movements, operating speeds, acceleration, etc. of the equipment vary during the operating processes. In conventional manufacturing, skilled workers must adjust the operating parameters according to various specifications, such as the required level of accuracy. Mitsubishi Electric has now developed an AI technology that simultaneously performs high-speed inferences and equipment control for real-time FA operation. Incorporating Mitsubishi Electric’s expertise as an FA equipment manufacturer, the new low-load AI control technology performs inferences while simultaneously controlling FA equipment. Although the technology minimises its processing load, it is capable of achieving high-level inference accuracy while simultaneously guiding FA equipment control.
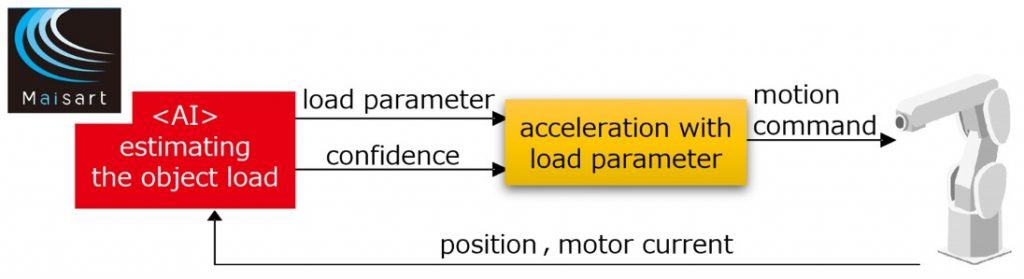
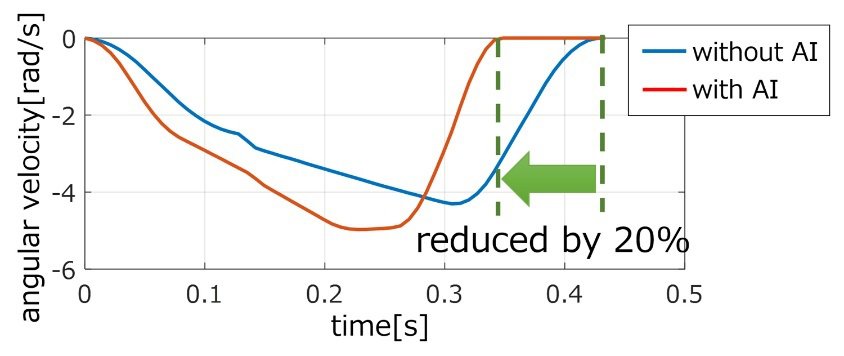
- Adaptable: In-process learning to adapt to constantly changing work factors
The shapes of workpieces change during manufacturing, and this can lengthen manufacturing times or lower processing quality. In addition, changes can vary by workpiece, making it difficult for FA equipment to learn in advance. Mitsubishi Electric’s new technology, however, allows the AI to learn work factors during FA equipment operation and then make real-time adjustments as needed. In addition, the technology formulates physical phenomena, such as friction, and then incorporates these mathematical expressions to enable learning during operation, making it possible to adapt to constantly changing processing factors.
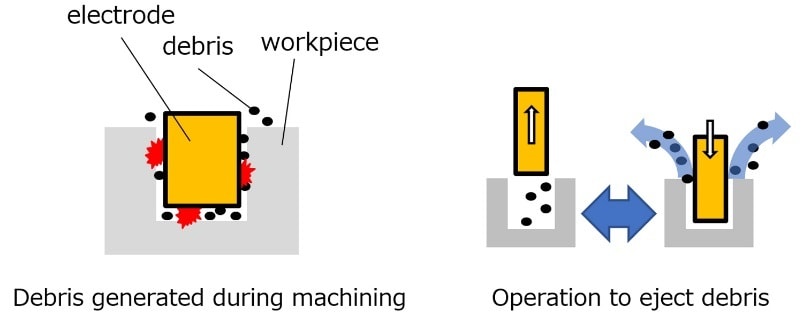
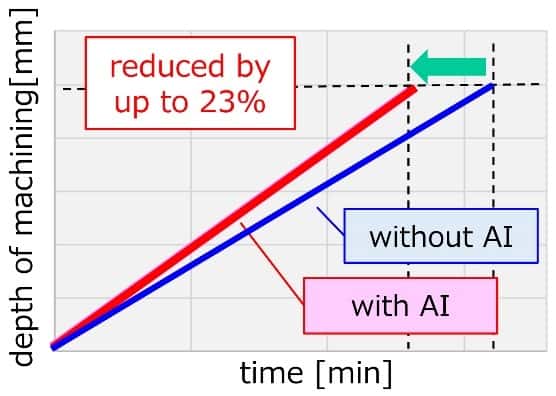
- Reliable: AI performs adjustments according to inference-confidence levels
AI inferences must be reliable to ensure that real-time control of FA equipment leads to stable product quality and efficient processing. Mitsubishi Electric’s new algorithm calculates the confidence level of inferences by learning the machine characteristics of each process and each target device. By using this algorithm to control FA devices, the new AI ensures high reliability.
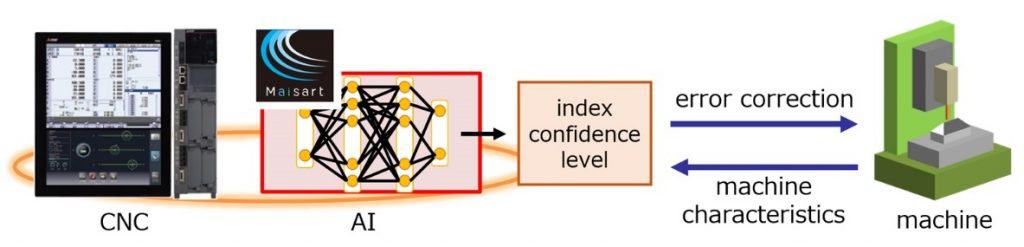
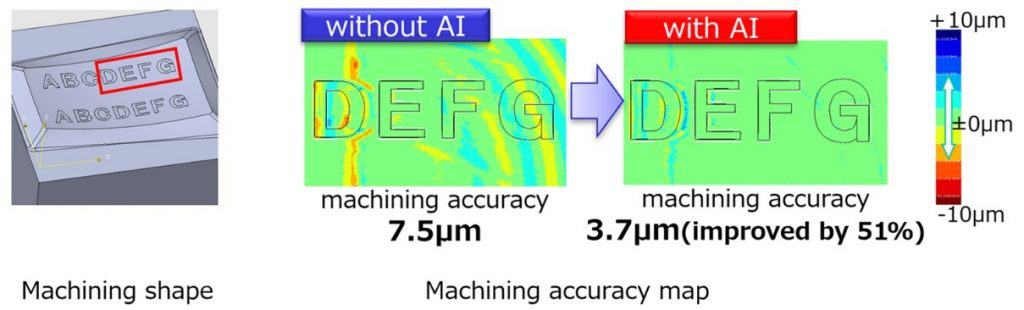