Years ago, I worked at a semiconductor packaged fabrication company. I’d regularly receive reports about machinery failure and the occasional accidents related mostly to the use of machinery that produces plastic or ceramic packaging.
Each ‘accident’ would equate to downtime for the entire production line which would, in turn, lead to delays in delivering the final product to customers. You can imagine the behind-closed-door meetings trying to figure what happened and how to avoid similar incidents in the future.
The true cost of downtime
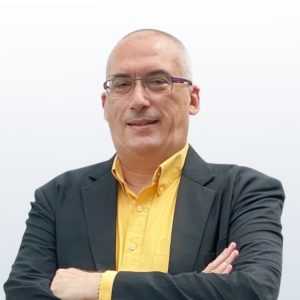
Alain Dupuis, VP Industrial Development at UnaBiz acknowledged that nothing is ever simple when it comes to estimating the cost of downtime.
“It varies greatly, from a minor annoyance to catastrophic proportion. What is difficult to evaluate is the rippling effect of one downtime over a whole process. Sometimes a small downtime can have severe consequences down the line,” he elaborated.
Those were the days when rudimentary controls were the prevailing technology, and any automation would be prehistoric by today’s standards.
Persistent downtime
Advances in IoT and industrial automation have evolved to the point that today there is a potential to significantly improve efficiency and safety through predictive maintenance.
However, Dupuis pointed out that very few aspects are currently addressed by technology.
“It is still a long way before we have implemented across it the board. There is a major cost involved to cover all the aspects and despite the best advancements in technology AI cannot do everything so it will never be 100% foolproof,” he added.
Understanding the AI equation
Given all the technology innovations, particularly the injection of Industrial Internet of Things (IIoT) technology into the production facility, for example, why do downtimes still exist?
For Dupuis, the most important action item is developing a proper digital model of a business operation through the interaction of all the processes involved.
“Then run AI through this model fed by real-time information from IoT nodes to detect bottlenecks early and balance the load between processes to remove potential showstoppers and streamline the operations. After this, use the AI to work on improving the processes themselves,” he continued.
He cautioned that one of the issues with AI is that it needs examples of failures to define what success is. For example, in predictive maintenance for a water pump, the AI needs to know what are the signals that say that the pump will break.
“Not many businesses will want or can afford to break something just to make their AI work faster and better. So, the implementation of AI in most cases can be a long process before reaching its effectiveness,” he opined.
To AI or not to AI
The quest to modernize a production line is not as simple as introducing new software. Any changes will incur costs such as a planned downtime while the new technology is being introduced to the process and the people that need time to learn to use the technology.
Dupuis highlights the very first challenge – complexity!
This is the paradox of modernization: the more you try to simplify the process, the more sophisticated the technology needs to make it happen.
“For AI to work you need a lot of things to be put into place. AI is kind of the last thing you will add when you have already a strong data collection system only when a massive amount of data is collected over time, can insights be drawn, and Machine Learning and AI come in.
“For this, you need IoT to be implemented at a massive scale. Then, you need it to relate to the enterprise IT system. This requires a lot of dedication and know-how which often companies do not have internally and with little external consultancy available for help,” he added.
Dupuis raised the second thing is cost. “All this complexity requires a heavy investment, in capital and human resources. The third aspect is linked to the second, a lack of confidence regarding the return on investment. AI is still a very new thing, and it is often difficult to measure the potential benefits,” he said matter-of-factly.
Questions to ask
Because everything involves an investment – whether it is time or resources – there should be sufficient understanding about what is involved and how it will impact people, processes and the business.
Dupuis agreed that people need to be honest with themselves in looking at the major pain points that affect running their business. He suggested going about this along with a comprehensive risk analysis.
“What needs to be put forward are those with either high recurring occurrences and/or with potential major destructive effects. Then focus on the top pain point and risk and start with this,” he continued.
He explained that this will limit the expenses and maximize the ROI. Only then to approach this effort using both Agile and Design Thinking methodologies.
“Do not look at it as a one-off effort but as a continuous work where improvements will be made along the way through refinement of the model and with the integration of new services as you will be answering more pain points and risks along the way,” he continued.
According to Dupuis, the question they need to ask themselves is: ‘Are we ready and willing to commit to digital transformation?’
“When it comes to selecting their service providers, they should avoid vendors pushing ready-made "universal" solutions even if they look like good deals at first glance. They want to choose a service provider that is listening to them and offering a tailored service because they know that every business is different. Never forget that this is going to be a very long-term work relationship,” he concluded.